With the spread of horizontal drilling around 2013-15, the artificial lift landscape began to change. For almost 100 years most wells had started the production phase with a beam pump (pumpjack) and finished with the same. Horizontal wells are a more complex beast, as production levels drop significantly over a well’s life. Changing production levels require either different lift methods over time, or one pump flexible enough to handle a wide range of flow rates.
Companies like Liberty Lift and Baker Hughes have adapted their business models to stay ahead of the curve—and that curve is swaying faster than ever in 2022.
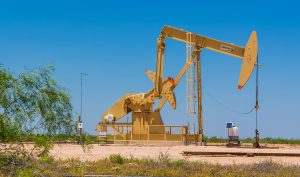
Liberty Lift west Texas. EG Unit.
Said Liberty Lift Vice President Don Crow, “Ten years ago, when we started this company, everything was being drilled vertically. They drilled a well, they completed the well, and you put a pumping unit on it. That’s the way the pumping unit business worked.”
But shortly after the shale revolution started, needs began to evolve. “It completely changed the landscape of artificial lift,” Crow recalled. This was particularly true in the Delaware Basin. It was back to school for the industry as a whole, learning the nuances of producing oil from laterals instead of a straight vertical hole. Also, greater amounts of gas created gas-locking issues, and increasingly longer laterals brought other challenges, which producers and service companies worked through.

Instead of installing a pump jack within a month of completion, as with a vertical well, the horizontals often went three years before needing a pumping unit, Crow said. “It completely changed our thought process. They were drilling these horizontal Delawares and they’d flow for a while, then they’d put ESPs [electric submersible pumps] on for a while, then they would either put on gas lift or a pumping unit.”
Crow cited a recent Kimberlite Research survey showing that only 16 percent of respondents used a single form of artificial lift through the life of a horizontal well. Producers using two forms of lift constituted 59 percent, while the remaining 25 percent reported using three different systems. Of the last group, he said most start with ESP, progress to gas lift, then finally go to the trusty rod lift.
Even rod lift has changed, with the company’s long stroke unit, the XL, offering stroke lengths of 291 inches to 416 inches, which they install on horizontal wells in the Permian Basin. That lets producers “get away from the ESPs earlier in the cycle,” he said. He explained the early change by the fact that ESPs, while prolific producers, can be prone to gas interference, susceptible to damage from wellbore debris, and are costly to replace.
Liberty Lift has expanded in other ways in response to the increased selection requirements. “Now we’re offering gas lift, jet pumps, sucker rods, plunger lift, automation, and downhole pumps.” Not only is there a market for all that equipment, there’s an increasing need for input on how to determine which lift to start with, and how to know when to make a change. The company is also equipped to offer such information. “The only thing we do not currently have is ESPs,” he said.
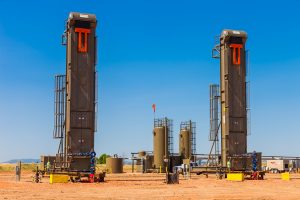
Liberty Lift’s XL Long Stroke Units, which have stroke lengths ranging between 291 inches and 416 inches, work well on horizontal wells.
One of the things affecting pump change decisions is the marketplace, Crow explained. “When oil was at $100-plus, we saw a lot of customers—even if an ESP was starting to have problems—they didn’t want to convert it because they would not want to lose any oil at $100 a barrel.”
If 2023 sees a continuation of prices in the $80 range, he believes producers will convert more wells to gas lift or pumping units.
Realizing that they continue to learn on a daily basis, Crow recalled the biggest single lesson of the last few years. “What we are really coaching customers on right now is to do as good a cleanout as you possibly can on the front-end, to minimize a lot of this trash—sand or whatever—that’s going up through pumps.” This makes pumps of all types last longer.”
Crow noted that automation is almost a necessity today, from a simple pump off controller to more complex systems. He sees many producers installing variable speed drives (VSDs) to increase efficiency and to manage power. The company is keeping up with those needs.
The One Pump Solution
Baker Hughes decided in around 2014-15 to make a single ESP with a wide enough production range that it would remain useful across a horizontal well’s life.
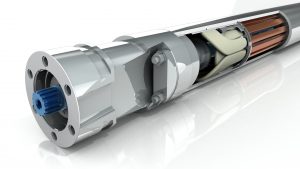
Baker Hughes’ Magnefficient Permanent Magnet Motor (PMM) significantly improves efficiency by lowering electrical submersible pumping (ESP) system energy consumption, allowing producers to do more with less.
Realizing that unconventional wells were a different animal, Bob Laird, the company’s director of technology for artificial lift systems, said Baker Hughes Artificial Lift Systems (“ALS”) “introduced a the FLEXpumpER Extended Range Pump technology which effectively widens the operating range of the pump (an ESP), making it useful over a much wider production range..”
Operators, he said, had one goal, to keep the same pump in the hole from the start until it wears out. They had no interest in repeated expenses involved in resizing across the well’s decline curve.
In addition to longevity, the pump needed to manage the increasing amount of natural gas involved as the well’s production cycle continues. “We had some tremendous success in that space with our products,” Laird said. Their FLEXpumpER Extended Range Pump and CENesis PHASE multiphase encapsulated production solution are designed to handle large volumes of gas and wide production ranges. “Those technologies help to reduce interventions, and associated costs, due to resizing of equipment,” Laird said.
Laird noted one of the biggest changes ushered in by the COVID shutdowns was that operators were forced to focus more on costs, which made them review their operational efficiency. In particular, “In the Permian, power to operate an ESP is a major cost consideration and opportunity.” One major in particular, he recalled, listed their electricity costs across the Basin for just ESPs at $80-90 million per year. So, “If they could get a 10 percent reduction in power consumption due to technology and efficiency improvements, they would save between $8 and $10 million. That seems pretty significant.
“In addition to that, if they can get it [the ESP] to run longer because we have a better fit-for-purpose tool—like the pumps, or a high-efficiency motor—they can even reduce costs further.” Dropping power consumption not only cuts the power bill, he explained, it can also allow more pumps to run off one power grid, which slashes infrastructure costs as well. And, he added, those savings continue through the entire life of the well.
Another way to reduce power costs is by replacing induction motors with permanent magnet motors to drive ESPs, an upgrade that is starting to gain traction in the Permian Basin. “Permanent magnet motors [PMMs] provide efficiency and are shorter, due to power density improvement,” Laird said. “They also require less electricity and have a flatter efficiency curve, creating higher performance over a wider operating load. Given this efficiency, PMMs run inherently cooler, which further increases ESP longevity.
The pump system’s reliability is important in lengthening run life and reducing well intervention frequency. “Identifying the root cause of a failure is critical in providing a solution/corrective action to extend the pump system’s life and reducing the TCO [total cost of ownership],” he pointed out.
Through a holistic approach, combining computation fluid dynamics, mechanical design, and design for manufacturing technique, the company has achieved greater stage performance efficiency than was previously possible. Baker Hughes LiftPrime pumps show that these technologies can be game-changers regarding end-user performance and reliability. “We’ve developed a highly efficient system, called CENEfficient, which combines LiftPrime pump technology and Magnefficient Permanent Magnet Motor technology. These systems are more reliable and efficient than standard options. Higher efficiency systems also emit less carbon. It’s a smart solution that is a win/win for the operators and the environment.
“One of the big spaces that everybody’s talking about is on the digital side,” he observed. “Digital’s not just monitoring and surveillance—it’s automation. It’s using analytics to predict failures so that you can plan better.”
With predictive analytics, a producer with hundreds or thousands of ESP wells can get an idea of which ones may be the next one to need servicing or replacing. While it is still a work in progress, our data analytics applications can extend run life and provide operators with predictability in planning well interventions.
The exact meaning of AI is often misunderstood, Laird noted. A professional paper he recently heard in a presentation defined it as when “you want the machine to act like a human,” he said. “It’s not just monitoring—the machine needs to act like a human would, given that set of data. That’s a big space people are moving into right now, and we’re certainly moving into that space.”
AI can monitor a pump’s performance in real time and make adjustments that can extend run life, as the AI “learns” over time. It also makes production engineers more efficient. A production engineer today can handle many more wells than was possible 10 years ago.
Labs are important, Laird said—they’re where engineers work to upgrade and improve technology that makes pumps last longer, provide better data, and boost efficiencies. “But solutions are born in the field where operators experience problems and create ideas to solve them. Understanding the cause of the problem and subsequent failures is vital in developing technology to overcome the failure mode. Solving run life problems improve the economics for operators and helps to build confidence in product performance for a given application.
_________________________________________________________________________________________________
By Paul Wiseman
https://pboilandgasmagazine.com/pumping-black-gold/”>
#Pumping #Black #Gold #Permian #Basin #Oil #Gas #Magazine